Modernised kiln control system at Tata Steel addresses obsolescence and enables a future Connected Enterprise.
InControl Systems deployed a new Rockwell Automation control solution in less than 16 hours per kiln, delivering the data capabilities of the contemporary control architecture.
The Company
Tata Steel’s limestone quarry and lime kilns, located in Cumbria in the UK, have been producing quicklime and limestone products since 1962. At the plant in Shapfell, the company produces high-performance lime products created to meet the requirements of a wide range of applications. Lime products include CE-marked fine lime, other size grades, and ground limestone in flexible quantities and at short notice.
The Problem
In a past audit, Tata Steel realised that the control infrastructure managing four of its Maerz lime kilns was at the end of its lifecycle and was effectively obsolete. As well as facing potential operational failure risks associated with obsolete hardware, Tata Steel was seeing increased maintenance costs and diminishing performance levels. It had a problem with alarming too, not only in terms of the number of alarms but also with regard to how to effectively manage them. Easier connectivity to the rest of the plant would also be of huge benefit, allowing Tata Steel to exploit the capabilities of future Connected Enterprise opportunities. As a result, the control system had to be replaced as a matter of urgency.
After a rigorous vetting process, it opted for a Rockwell Automation based solution designed and delivered by InControl Systems lining began to degrade – in this case less than 16 hours. Any longer and the bill for repair could run into many thousands of pounds.
The Solution
Prior to the installation of the new contemporary system, a fully simulated environment was built and run within the ControlLogix PAC, which mimicked the way the kilns worked, simulating the process conditions offline. PlantPAx process control system faceplates were also used and modified to meet the Tata Steel standards.
“We then gave this to Tata Steel, to let its engineers run and test the new solution and deliberately create faults to see how it handled the alarms. Their feedback then allowed us to fine-tune and refine the control system before we put it anywhere near the kilns. This virtual testing using VMware-compliant Rockwell Automation software allows us to do an incredible amount of offline testing but using real-life parameters.” – Jan Hemper, Technical Director at InControl.
Virtual testing is much easier and a lot faster than on-site testing and delivers greater peace of mind to the customer. In addition to the refinement, the virtual environment also proved ideal for training, so the engineers at Tata Steel were already up to speed before the hardware was rolled out.
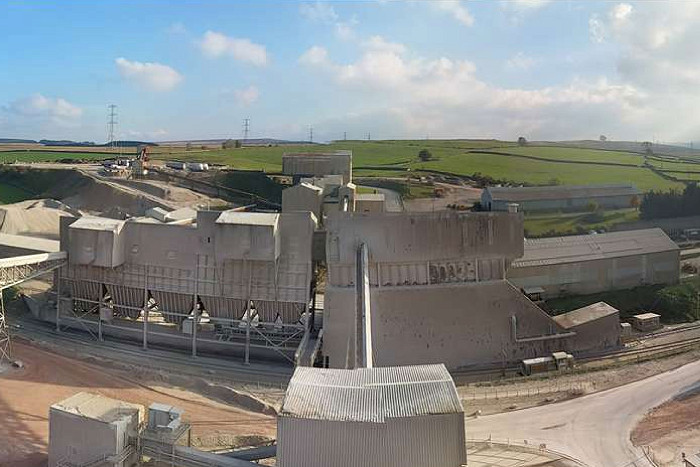
The Results
Since the installation, the new control solution has been working as designed and has proven to be a more than capable replacement for the older system. Along with the significantly reduced risk of failures, Tata Steel is also seeing many other benefits of a contemporary control solution. These include far more effective data management, thanks to FactoryTalk Historian; the effective collection and collation of real-time data, allowing the company to make better informed role-based business decisions; and clearer data presentation and disbursement thanks to FactoryTalk VantagePoint.
The use of an EtherNet/IP communication backbone has also allowed Tata Steel to exploit the power of The Connected Enterprise. The new control solution not only connects to the site’s ERP system, but also to its quality system, laboratories, and its road & rail logistics system. The use of an EtherNet/IP-based communication protocol also gives InControl the ability to ‘dial in’ to the site to remedy any issues without having to undertake costly engineering visits.
“A lot of people are wary of letting you touch their kilns. If you wreck the refractories, it costs thousands to fix. We have proven that modern control solutions can be implemented in incredibly short time windows and at a very attractive price point. We have now modernized four kilns at Shapfell and are eager to let other Maerz kiln operators know that we now have a standard tried-and-tested solution.” – Jan Hemper, Technical Director at InControl.
“We needed a solution that would offer us good reliability that could help us replace the older system in stages without disrupting the production. We also went for a system that would be supported by readily available spares and one that could deliver remote support. The Rockwell Automation-based solution ticked all the boxes. We are now seeing more real-time information, so trending is a lot more straightforward. The next stage will be to look at increasing efficiencies at the plant, which will be more straightforward thanks to our new data capabilities and the ability to easily add more hardware.” – Ian Busby, Engineering Manager at Tata Steel’s Shapfell plant.